【关键词】黏土;羼和料;古代制陶原料
【摘 要】中国古代的制陶原料有黏土、羼和料两大类。根据光谱测定和化学分析的结果,可将制陶原料中的黏土分为普通易熔黏土、高铝质耐火黏土、高硅质黏土、高镁质易熔黏土;因羼和料不同,古代陶器除泥质陶外,还有夹砂陶、夹云母陶、夹蚌陶、夹骨屑陶、夹炭陶和夹陶末陶等。其中“高硅质黏土”的概念比较重要,可将印纹硬陶与原始瓷区分为两类不同的产品:制作印纹硬陶的原料是高硅质黏土,而原始瓷制胎的原料是瓷石类岩状矿物。
制陶工艺流程包括原料制备、坯体成型、坯体修整、坯体装饰、陶器烧制、烧制后装饰(指彩绘陶)等六道工序。其中,原料制备是工艺流程的基础,如果第一步走错,就会步步走错,对古人来说制陶不会成功,对今人来说,研究古代制陶工艺也不会成功。制陶原料研究的重要性就在于此。
中国古代的制陶原料有黏土、羼和料两大类。根据研究课题的需要,考古工作者将出土层位可靠的典型陶片提供给科技工作者进行检测。科技工作者采用光谱测定、化学分析等科技方法对陶片进行检测,得到了大量数据。本文依据这些数据,分别对古代制陶所用的黏土、羼和料进行分析。
黏土
黏土是制陶不可或缺的原料,因为它有黏性,加水后有可塑性,与羼和料之间有结合性,在制陶工艺上称之为“塑性原料”。沙土是由大量的沙和少量的黏土混合而成的土,由于沙土缺乏黏性、可塑性和结合性,不能作为制陶原料。
黏土中的主要化学成分为氧化硅(SiO2)、氧化铝(Al2O3),另有少量氧化铁(Fe2O3)、氧化亚铁(FeO)、氧化钛(TiO2)、氧化钙(CaO)、氧化镁(MgO)、氧化钾(K2O)、氧化钠(Na2O)、氧化锰(MnO)、氧化磷(P2O5),统称为“助熔剂”(由于氧化锰、氧化磷的含量不高,平时不计算在助熔剂总和之内)。
黏土的颗粒越小,黏性越大,可塑性越好,结合性越好,坯体的干燥收缩率越高。从制陶原料角度,可按化学组成含量的不同,将黏土分为普通易熔黏土、高铝质耐火黏土、高硅质黏土、高镁质易熔黏土四类。其中以普通易熔黏土最常见,高镁质易熔黏土最少。
(一)普通易熔黏土
普通易熔黏土的化学组成以低氧化硅、低氧化铝、高助熔剂为特征。“普通易熔黏土”即一般的易熔黏土,与“高镁质易熔黏土”相比,后者氧化镁的含量格外高。“高助熔剂”有助于降低氧化硅和氧化铝的熔化温度(即熔点),有助于黏土的烧结(即把粉状物料转变为致密体),把坯体转变为陶器。
例如表一中所列湖北宜都市城背溪、枝城北遗址出土城背溪文化新石器时代中期陶器,编号为 2、3、4、6、7 的标本其氧化硅占比52.76% ~67.15% ,氧 化 铝 占 比 16.60%~20.09%,助熔剂(Fe2O3、FeO、CaO、MgO、K2O、Na2O)总和占比 11.22%~14.36%,属于普通易熔黏土。
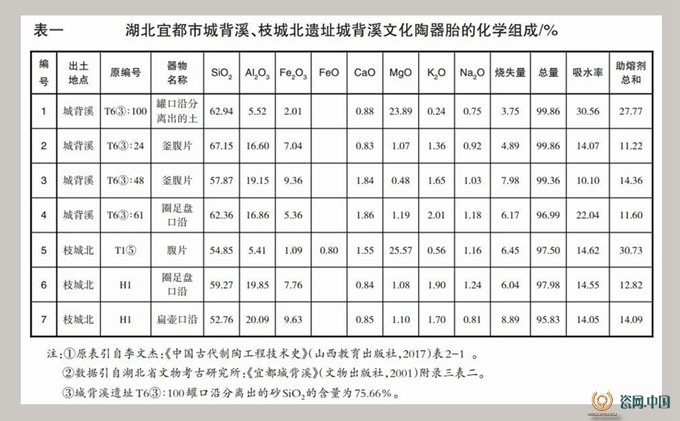
(二)高铝质耐火黏土
高铝质耐火黏土的化学组成以低氧化硅、高氧化铝、低助熔剂为特征。因为氧化铝的熔点为 2054℃,是耐火材料,所以这类黏土称为高铝质耐火黏土。
学术界对“高铝”的含义并无严格界定,承蒙中国科学院自然科学史研究所何堂坤先生于2010年当面告诉笔者,他认为可以暂将氧化铝含量大于 22%者视为高铝质耐火黏土和高铝陶。他曾统计过6件新石器时代晚期至铜石并用时代的高铝陶的成分,其氧化铝含量为22.12%~29.38% ,平均值为26.32%;还统计过51件同一时期的南方和北方的普通易熔黏土陶胎的成分,其氧化铝含量为10.60%~21.41%,平均值为17.03%。依此,“22%”恰好处于6件高铝陶标本氧化铝含量的下限附近,51件普通易熔黏土标本氧化铝含量的上限附近。
表二为山东章丘市城子崖遗址出土的山东龙山文化白陶的化学成分检测数据,其氧化铝平均值为 29.68%,表明其制胎所用原料属于高铝质耐火黏土。高铝质白陶的质地较硬,手摸器表没有滑腻感。这种白陶与后世瓷器制胎的原料有关,从制胎原料角度说,高铝质白陶是瓷器的前身。
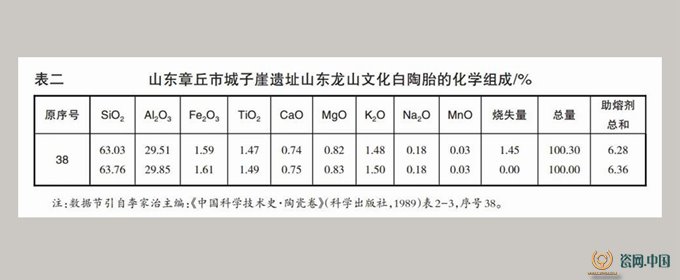
(三)高硅质黏土
高硅质黏土的化学组成以高氧化硅、低氧化铝、低助熔剂为特征。笔者认为,这类高硅质黏土主要存在于南方地区,主要充当制作印纹硬陶的原料,然而又和后来普遍用于制瓷、同为高硅成分的瓷石类原料存在差别。
印纹硬陶是指外表有拍印或滚印而成的纹饰、烧成温度高、质地坚硬、吸水率低的陶器,广泛分布于江西、江苏、上海、安徽、浙江、福建、台湾、湖北、湖南、广东、广西等地,其中江西是印纹硬陶工艺的中心和发祥地。印纹硬陶最早出现于江西清江县(今樟树市)筑卫城中层,相当于中原地区的夏代,发展于商代,盛行于西周,春秋晚期开始走下坡路,到战国时期衰落,汉代则逐渐被原始瓷取代。
表三所列为江西清江县(今樟树市)吴城出土商代印纹硬陶的化学成分检测数据,其中氧化硅占比 67.64%~80.08%(大多数在70%以上),氧化铝占比 11.82%~22.04%(大多数在22%以下),助熔剂(Fe2O3、TiO2、CaO、MgO、K2O、Na2O)总和占比 6.51%~9.96%。可以断定,印纹硬陶是以高硅质黏土为原料。
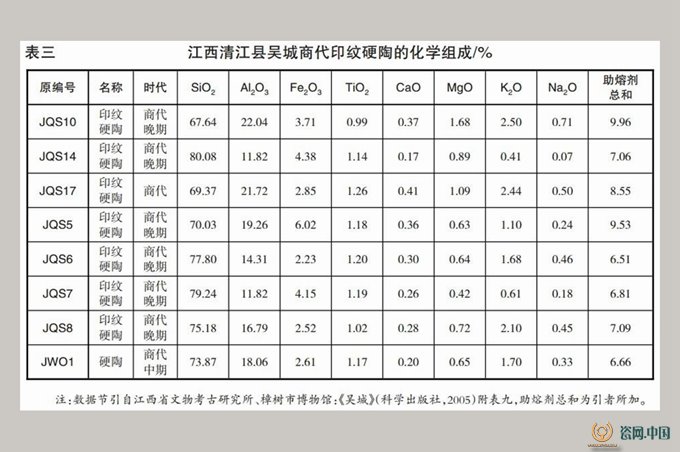
印纹硬陶在原料选择、坯体成型、整形和装饰、陶器烧制诸方面具有独特性:
1.印纹硬陶和原始瓷是两类不同的产品,制胎原料不同
原始瓷是以瓷石为原料,印纹硬陶是以高硅质黏土为原料。瓷石与高硅质黏土相比,其性状明显不同:瓷石是岩状矿物,而高硅质黏土是土状矿物。由于性状不同,其加工方法也不同,笔者通过景德镇陶瓷大学的郁永彬先生了解到:近现代的景德镇制瓷工艺中,瓷石要用水碓粉碎后方可使用,而高硅质黏土经过筛选即可使用。
2.印纹硬陶和原始瓷的成型方法不同
经观察,出土印纹硬陶均采用泥条筑成法成型。2013年,笔者曾仔细观察了中国国家博物馆馆藏的分别出土于上海、福建、广东的6件印纹硬陶(商代4件,春秋2件),确认其中2件采用泥条盘筑法成型,4件采用泥条圈筑法成型。泥条盘筑法和泥条圈筑法总称为泥条筑成法。有考古工作者发现,“在印纹陶和原始瓷合烧的窑址中,原始瓷采用轮制术,印纹陶仍用泥条叠筑法”。也有学者在考察了江西出土的印纹陶后认为其成型采用“泥条盘筑法”。由此可见,各地区、各时代的印纹硬陶几乎都采用泥条筑成法成型。
众所周知,除一些边疆地区和少数民族地区外,汉代的陶工一般都已熟练地掌握了快轮制陶技术。快轮与慢轮之间在构造上存在质的差别。慢轮由于构造上有缺陷,不能作为快轮使用,但快轮可以两用:快速旋转时可以将泥料直接拉坯成型,慢速旋转时可以在轮盘上用泥条筑成坯体。汉代的陶工在制作其它圆形陶器时都采用快速旋转、拉坯成型的方法,唯独制作印纹硬陶时要采用慢速旋转、泥条筑成的方法。原因是,高硅质黏土泥料可塑性范围狭窄(也是缺点),只发生在含水率为 22%~19%的范围内,而拉坯成型适宜的含水率为26%~25%,因而达不到拉坯的要求(提拉不起来,更谈不上成型),只能采用泥条筑成法成型。快轮慢用并非制陶技术的倒退,而是针对不同的泥料采用不同的旋转速度和成型方法,这恰好反映了陶工随机应变的灵活性和聪明才智。
3.印纹是整形工序中的“副产品”
泥条筑成的坯体,经过拍打或滚压整形,才能消除泥条缝隙,提高坯体的致密度,以免在干燥收缩和烧成收缩过程中开裂。就印纹陶来说,整形的同时产生拍印或滚印的纹饰,兼有装饰作用。
4.印纹硬陶烧成温度比较高
高硅质黏土泥料的耐火度较高(这是优点),因为氧化硅的熔点为 1713℃,仅次于氧化铝的熔点(2054℃)。40多年前,笔者曾调查过湖北枝江县陶器厂(位于枝江县城西27公里的善溪窑)利用当地产的一种黏土烧制的高温釉陶泡菜坛子:测出的黏土耐火度为1140℃,素胎采用的烧成温度为 1120℃,低于耐火度 20℃,这样做既提高了素胎的硬度和强度,又可防止素胎烧流变形。笔者根据硬度估计中国国家博物馆馆藏印纹硬陶的烧成温度为 1050~1100℃。出土的印纹硬陶都是在窑温较高的陶窑尤其是平焰窑内烧制而成的。
印纹硬陶在原料选择、坯体成型、整形和装饰、陶器烧制诸方面具有独特的工艺规律,各道工序之间具有内在联系,甚至有因果关系,既克服了高硅质黏土可塑性范围狭窄的缺点,又发挥了高硅质黏土耐火度较高的优点。
希望未来考古工作者和科技工作者能关注南方地区高硅质黏土和瓷石类岩状矿物两类原料来源地的不同地貌情况,以查明二者之间的差别。
(四)高镁质易熔黏土
高镁质易熔黏土的化学组成以低氧化硅、贫氧化铝、富氧化镁、高助熔剂为特征。在这类黏 土中 ,氧化镁的含量一般达到20%。氧化镁有两种性质:一种是熔点高,达2852℃,是碱性耐火材料,作为耐火材料时氧化镁的含量在 80%以上;另一种是在烧制陶器过程中具有碱性助熔剂的作用。从耐火材料转变为助熔剂是由量变到质变的过程,与氧化镁的含量从 80%以上降至临界点附近有关。因为氧化镁具有助熔剂的作用,所以将富含氧化镁的黏土称为高镁质易熔黏土。
例如新石器时代中期,表一所示编号为1、5 的分别出土于湖北宜都市城背溪、枝城北遗址城背溪文化的两件陶器(T6③∶100和T1 ⑤),其 氧 化 硅 占 比 分 别 为 62.94% 、54.85%,氧化铝占比分别为 5.52%、5.41%,氧化镁占比分别为 23.89%、25.57%,助熔剂总和占比分别为 27.77%、30.73%。又如新石器时代晚期,湖北枝江市关庙山遗址出土的大溪文化的一种白陶 ,氧化硅占比67.79%~68.92% ,氧化铝占比3.28%~5.57%,氧化镁占比18.01%~23.38%,助熔剂总和占比 21.92%~25.93%。这两例都以高镁质易熔黏土为原料。高镁质白陶独有的特征是:手摸器表有滑腻感(有摸滑石的感觉),质地较软,用指甲刻划器表会掉粉末。这种白陶与后世瓷器制胎的原料无关,不是瓷器的前身。
羼和料
羼和料是人工羼入陶土内的辅助性原料,其特点是没有黏性,在制陶工艺上称之为“瘠性原料”。可分为四类:矿物类(有石英、长石、云母等)、动物类(有蚌壳和螺壳碎片、骨屑)、植物类(炭化稻壳)、陶类(陶末)等。
黏土与羼和料按照适当比例(从体积上说,约3∶1至5∶1)配制使用。配制方法有两种:一种是先将两类原料掺和在一起,加水润湿透彻后,用手揉练或用脚踩踏成为泥料;另一种是先将黏土加水练成泥料,后加入羼和料,再揉练至羼和料分布均匀,与黏土紧密结合。
羼和料的主要作用是:减少塑性原料的黏性,便于坯体成型;起筋骨作用,增加坯体的强度;对于炊器来说,可增强耐温度剧变的性能,防止烧火使用时开裂。
(一)夹砂陶
夹砂陶是以砂粒作为羼和料的陶器。砂粒种类包括石英砂、长石砂、石灰岩砂、方解石砂等:以石英砂为最佳,其摩斯硬度为7,耐磨损,主要成分氧化硅的熔点为1713℃,耐高温;以石灰岩砂和方解石砂最差,其主要成分是碳酸钙(CaCO3),在高温下会分解,伤害陶胎。新石器时代早期的陶器都是在低温中烧成,碳酸钙不会分解,因此石灰岩砂和方解石砂也可以作为羼和料。
例如新石器时代中期,河南舞阳县贾湖遗址的陶器常用细砂作为羼和料,粒径约0.5毫米。城背溪文化的夹砂红陶,砂粒直径1~3 毫米不等;从夹砂白陶 T6③∶100 口沿分离出的砂粒氧化硅含量为 75.66%(表一注③),表明是石英砂。新石器时代晚期,湖北枝江市关庙山遗址大溪文化的夹砂陶,砂粒粗细因器类而异:尖底缸、陶臼和草帽形器座等大型厚胎器物含粗砂,小口高领罐、罐形鼎等器物含细砂。砂粒的主要成分是氧化硅,据枝江市水泥厂化验室分析,云池长江边的砂粒化学组成为:氧化硅 89.28%,氧化铝4.56%,氧化铁0.96%,氧化钙0.68%,氧化镁1.23%,烧失量2.36%,表明是石英砂。
夹砂陶的优点是坚固耐用,适宜作为盛储器和炊器;缺点是表面粗糙,不宜作为饮食器。
值得注意的是,铜石并用时代早期,山西垣曲县古城东关遗址出土庙底沟二期文化早期的某些陶斝上下两部分用不同的泥料制成,例如斝ⅠH251∶64、ⅠH262∶16,折棱以上至口沿为泥质,器表磨光,折棱以下的圜底及袋足夹细砂,具有耐温度剧变性能,整件器物达到了美观与实用的统一。
(二)夹云母陶
夹云母陶是以云母片作为羼和料的陶器。如北京市房山区镇江营遗址出土的新石器时代中期陶盆(H1022、T1309⑦),器表闪闪发亮,其羼和料呈现片状,经光谱定性分析,主量元素为硅,较多量元素为镁 ,少量元素为铝、铁,微量元素为钠、钾、钙、钒、镍、铬(表四),断定羼和料是一种含镁较多的云母片。遗址所在台地北部的黏土层之下发现含云母片的基岩,推测是羼和料的来源地。笔者将一块基岩砸碎后发现大量石子、砂粒、黏土,只有少量云母片,表明此地基岩是由多种矿物沉积而形成的次生矿物,先民就地取材,用砸碎基岩之后得到的云母片作为陶器的羼和料。笔者曾仿制了镇江营遗址第一期的夹云母陶釜,器表也闪闪发亮。
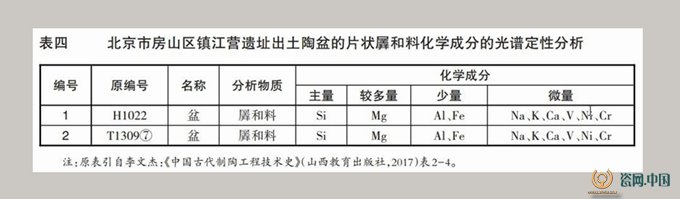
(三)夹蚌陶
夹蚌陶主要见于南方,是以蚌壳和螺壳碎片作为羼和料的陶器。新鲜的蚌壳或螺壳中含有碳酸钙和贝壳素(又称壳基质),以碳酸钙为主,贝壳素较少,因而质地坚硬,又有韧性。经笔者实验,直接用铁锤难以将蚌壳或螺壳砸成碎片状,经过小火烘烤,烧掉一部分贝壳素后就容易砸碎。先民用作羼和料的蚌壳和螺壳也应经过小火烘烤。
新石器时代晚期,湖北枝江市关庙山遗址大溪文化的夹蚌陶,从陶胎内蚌壳碎片的保存状况看,大致有三种情况:密实陶,氧化钙含量在 6.6%~9.61%之间,内壁、外表的蚌壳碎片已消失,留下凹坑,新的断面上可见蚌壳碎片(表五,1—3);半泡陶,氧化钙含量在4.12%~6.46%之间,破茬附近和内外表层都已变泡,陶胎深处仍存大量蚌壳碎片(表五,4、5),有些罐口沿的泡层与密实层之间有明显界线;泡陶,氧化钙含量为 2.05%~3.45%,数量较多,胎内有大量不规则形孔洞,强度低,容易破碎,内壁、外表状况与密实陶相同(表五,6—9)。因关庙山遗址的土壤pH值为 6.45~6.75,呈酸性,密实陶废弃后,与酸性土壤接触,被腐蚀后形成泡陶。
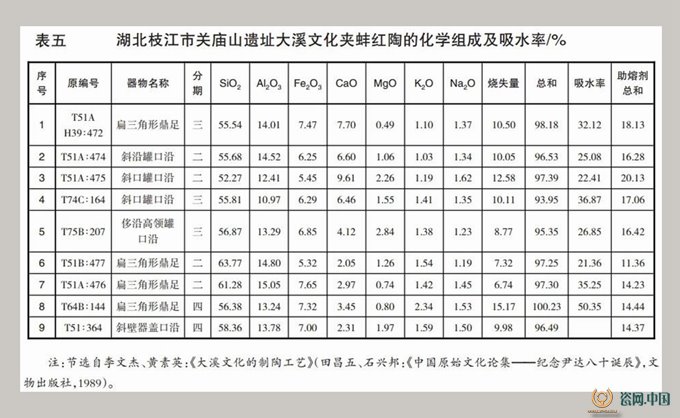
笔者曾就夹蚌陶进行了一些实验。
1984年笔者仿制的一批夹蚌陶,由于烧成温度不同,存放半年后的状况差异较大:烧成温度 840℃的器物胎壁胀裂酥散,蚌壳末变成了白色粉末;烧成温度 700℃的器物蚌壳末没有变成粉末,仍有亮光;烧成温度600℃的器物蚌壳末的亮光保存很好。
1985年笔者仿制了一件夹蚌罐坯体,在龙窑内用松柴烧制16小时,距火源80厘米,烧成温度约850℃,烧成后器表的蚌壳碎片已消失。将其浸在水中,胎心的蚌壳碎片吸水后逐渐膨胀,内外表层胎壁一块块剥落,表明蚌壳碎片已分解。
另外,笔者曾将关庙山遗址大溪文化第二期T51⑤A层的7片夹蚌红陶罐口沿(均为密实陶)置于马弗炉内,分别以温度 600℃、650℃、700℃、750℃、800℃、850℃、900℃复烧 ,并 保温一小时,存放半年后 ,复烧到850℃、900℃的2片口沿表面呈龟裂状,其余5片口沿保持原状。
从现代技术原理看,碳酸盐一般在700~800℃开始分解,900~1000℃开始沸腾,因此,夹蚌陶的烧成温度不宜超过碳酸盐开始分解的温度。古代夹蚌陶的烧成温度一般在700~800℃之间。如果烧成温度过高,蚌壳碎片内的碳酸钙会分解为氧化钙和二氧化碳,反应式为:CaCO3→CaO+CO2↑。氧化钙会逐渐吸收空气中的水蒸气,生成氢氧化钙,反应式为:CaO+H2O→Ca(OH)2,体积会逐渐膨胀,并变成粉末状。这种体积膨胀现象会产生很大的作用力,可使陶胎出现裂纹,表层一块块剥落,乃至整件陶器成为碎片。由此可见,严格地控制烧成温度的上限(800℃)是烧制夹蚌陶的关键。
(四)夹骨屑陶
夹骨屑陶是以兽骨碎屑作为羼和料的陶器。例如新石器时代中期,河南舞阳县贾湖遗址的一些陶器是将兽骨砸成碎块状作为羼和料,粒径约0.5~3毫米[7]。遗址中Y9旁发现经过火烧的骨屑堆,推测作为羼和料的骨屑应是先经火烧再砸碎。烧烤可以除去兽骨内一部分胶质,使其质地变脆,容易砸断、砸裂,成为碎屑。
(五)夹炭陶
夹炭陶是以炭化稻壳作为羼和料的陶器。炭化稻壳的主要成分是碳元素(C)。碳元素在常温下化学性质稳定,因此湖北枝江市关庙山遗址大溪文化的夹炭陶在土壤中埋藏了千年之久,其胎心内的炭末仍保存完好,没有出现孔隙。
学术界对稻壳作羼和料有两种看法:一种认为“在烧制过程中炭化”,另一种是“事先经过燃烧炭化”。笔者用关庙山遗址文化层之下的黄黏土作为塑性原料,分别掺入生的粗细两种稻壳及经炭化处理的稻壳,仿制成三批大小相同的倒梯形鼎足,烧成温度700℃,所得结果不同:用生的粗稻壳作为羼和料时坯体表面凹凸不平,炭化过程中收缩较多,炭末周围缩孔较大,鼎足机械强度较低,徒手即可折断;生的碎稻壳吸收泥料中的水分后韧性增强,练泥时不会折断,坯体表面出现毛刺,烧制后器表留有梭形碎稻壳痕迹,鼎足的机械强度略高于使用生的粗稻壳;炭化稻壳在练泥过程中被揉成头发渣状或粉末状,坯体表面平整,烧制时炭化稻壳收缩不多,从鼎足断面观察,炭末周围没有出现较大缩孔,鼎足的机械强度较高,用工具才能将其砸断。
模拟实验结果表明,用生的粗稻壳作为羼和料缺点较多,用炭化稻壳作为羼和料优点较多,而生的碎稻壳可以作为羼和料,但效果不如炭化稻壳。大溪文化居民以种植水稻为生,应熟知炭化稻壳的优点和生稻壳的缺点,制陶者自然会选择炭化稻壳作为羼和料。
(六)夹陶末陶
夹陶末陶是以陶末作为羼和料的陶器。陶末是将陶片砸成碎末状,制陶工艺上称之为“熟料”,复烧时膨胀系数较小,可以防止陶器开裂。目前所见最早的夹陶末陶是新石器时代早期江西万年县仙人洞遗址出土,用绳纹陶碎片作为羼和料,最晚的出土于甘肃、青海地区的辛店文化,年代相当于中原地区商周时期。
结语
上述事实表明,考古工作者仍需要多学些自然科学知识,运用交叉学科思维,充分利用光谱测定和化学分析及其他科技手段检测的结果,解决制陶原料研究中的问题。通过考古工作者与科技工作者的对话与沟通,本文将古代制陶原料分为普通易熔黏土、高铝质耐火黏土、高硅质黏土、高镁质易熔黏土四种,首次对不同黏土的特征做了解释,并对所用羼和料进行了分类。其中“高硅质黏土”概念的提出比较重要,可依此将印纹硬陶与原始瓷区分为两类不同的产品:制作印纹硬陶的原料是高硅质黏土,而原始瓷制胎的原料是瓷石类岩状矿物。(原文《古代制陶所用黏土及羼和料——兼及印纹硬陶与原始瓷原料的区别》刊于《文物春秋》2021年第1期,此处省略注释。作者:李文杰 中国国家博物馆。)